Porté et initié par Vincent Calleja, directeur général du groupe Tertu depuis 2018, le projet T.H2 prévoit la production de bioéthanol de deuxième génération puis d’hydrogène vert aux portes de Caen, à Blainville-sur-Orne.
L’objectif ? Revaloriser pas moins de 120 000 tonnes de déchets bois par an, et ainsi favoriser la mobilité verte en Normandie. Le tout avec une neutralité carbone de l’usine, comme du procédé. Portrait d’une innovation normande.
Des copeaux de bois à valoriser
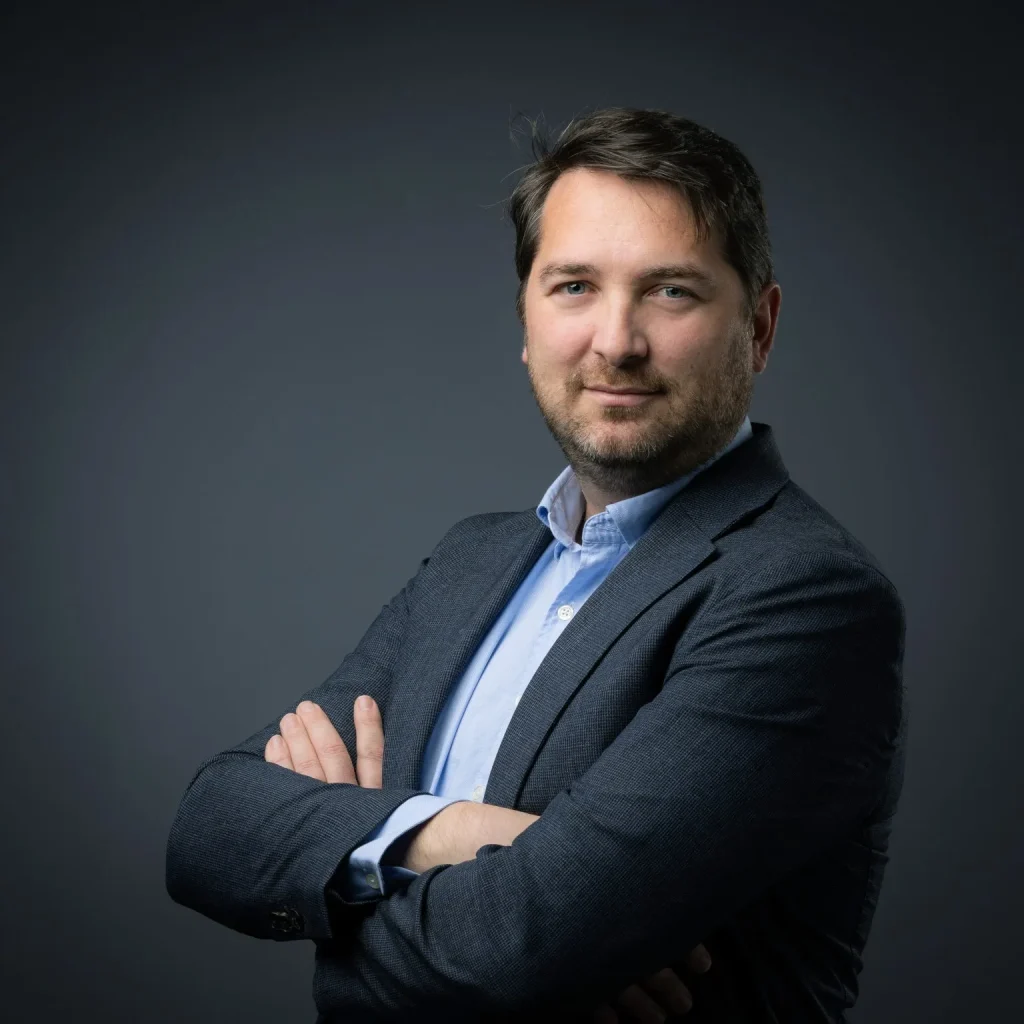
C’est désormais une fierté de l’entreprise ornaise, leader de la construction de glissières bois-métal, portée par l’ensemble des salariés, et menée tambour battant par son directeur général, Vincent Calleja.
Une fierté au nom de T.H2, pour Tertu Hydrogène.
A l’origine, comme souvent, un questionnement : que faire des copeaux de bois générés à hauteur d’1 à 2 semi-remorques par jour par la seule fabrication de glissières ? Comment offrir un nouveau débouché à ces produits naturels ?
Ils étaient déjà destinés à devenir des combustibles pour chaudières ou des panneaux de particules. Nous avions même créé une entreprise avec d’autres scieurs normands, Biocombustible, mais certains industriels n’ont plus souhaité faire appel à elle, j’ai donc réfléchi à une autre valorisation.
” Nous avons élargi le besoin aux nombreux déchets bois – avec de la peinture, de la colle, de la résine ou du produit de traitement – en bref des polluants issus de vieux meubles ou palettes usées “ souligne encore le directeur.
L’objectif ? Être innovant, disruptif et utile. Deux idées émergent notamment : faire de la résine biosourcée ou bien de l’hydrogène. C’est cette dernière qui séduit le jeune chef d’entreprise. ” En 2018, l’hydrogène vert ne parlait à personne. L’idée me plaisait parce qu’elle était folle. “
Une exclu, deux innovations en Normandie
” Je me suis engouffré là-dedans et à partir de 2018, j’ai parcouru le monde pour trouver une solution ” explique Vincent Calleja. Bureaux d’études divers et variés, tour du monde des technologies existantes…
En Inde, il découvre une technologie capable de transformer de la biomasse en gaz de synthèse ; aux États-Unis, c’est une société qui, à partir de gaz, nourrit des petites bactéries, les fait fermenter, et les distille pour faire du bioéthanol. ” C’était un laboratoire ultra-sécurisé avec 500 chercheurs capables de transformer le gaz en n’importe quelle molécule à partir de leurs bactéries et leur fermentation. “
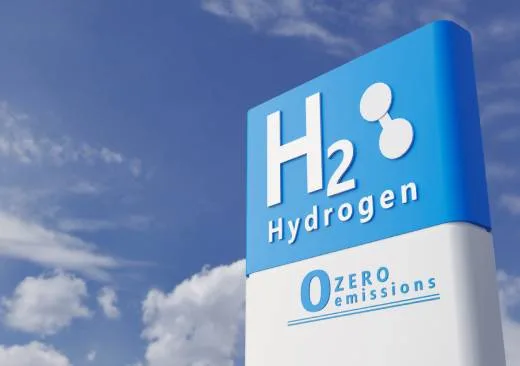
Un pari gagné pour Vincent Calleja qui combine ces deux innovations pour mener à bien son projet.
” Mon idée était donc d’associer la technique rustique indienne mais efficace avec la technologie américaine ultra pointue “. Fort de cette exclusivité, Vincent Calleja se concentre dans un premier temps sur l’hydrogène vert afin de le vendre. ” Mais le marché n’était pas mûr et en retour, l’éthanol revenait souvent comme un besoin dans la conversation. Cela m’a conduit à adapter mon projet. “
Son idée ? Garder le process de production d’hydrogène mais de le transformer in situ en bioéthanol, tout en gardant la capacité, demain, de revenir à la production d’hydrogène.
Nous, nous ne sommes qu’au niveau 1 de la bactérie : l’éthanol, c’est juste la transformation de la protéine en alcool, exactement ce que l’on fait en Normandie depuis des siècles, en prenant nos pommes pour en faire du calvados. C’est le même procédé.
Du bioéthanol seconde génération
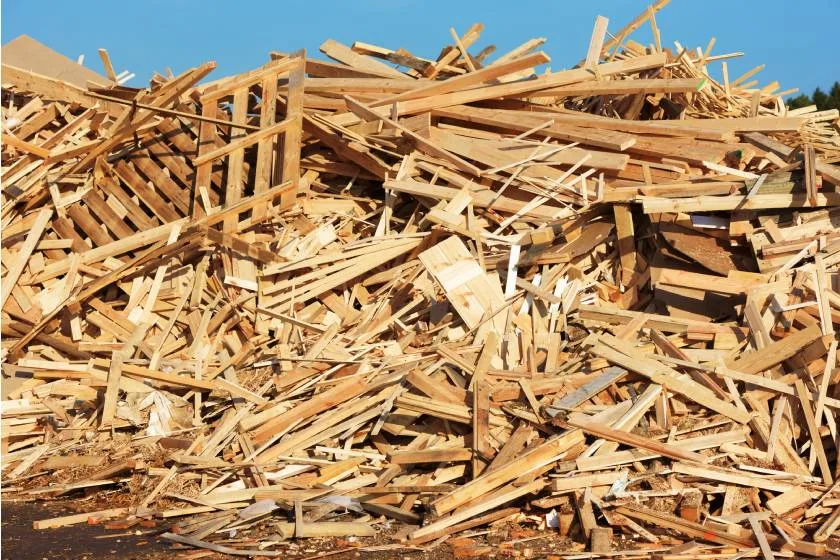
Produire du bioéthanol à partir de copeaux de bois, oui, mais pas n’importe lequel – on parle d’un bioéthanol de seconde génération.
” Le bioéthanol de 1ère génération provient de cultures agricoles destinées en premier lieu au marché alimentaire, comme la betterave ; le bioéthanol de 2nde génération capitalise sur la biomasse non alimentaire ; dans le cas de T.H2, il s’agit des déchets de bois revalorisés en biocarburant “ précise Vincent Calleja.
Le ratio, c’est environ 110 000 tonnes de bois pour faire 21 000 tonnes de bioéthanol ; le reste, c’est du biochar et du gaz.
Un choix également guidé par la réglementation puisque dans quelques années, la moitié des carburants devront être produits en 2nde génération. ” Aujourd’hui, la majeure partie est produite à partir de produits agricoles : le marché qui s’ouvre est donc gigantesque. “
Dès que l’annonce d’une production de ce bioéthanol de manière industrielle à venir s’officialise, en 2021, les demandes pleuvent : l’équivalent de 300% de la production prévue, estimée à 80 000 litres par jour.
Avec un marché supplémentaire : les groupes de luxe français, intéressés par le bioéthanol 2nde génération pour leurs parfums ou déodorants dans le cadre de leur démarche RSE.
Des procédés complexes et durables
Mais comment passe-t-on du bois au biocarburant ?
” On prend notre matière, le bois, que l’on porte à très haute température afin de casser son aspect moléculaire. Il en ressort une partie solide, que l’on appelle char et une autre partie que l’on appelle gaz de synthèse. C’est là que tout se joue “ explique Vincent Calleja.
Pour chaque étape du procédé qu’il a mis en place avec les cabinets d’études, une seule règle : essayer de reboucler et valoriser au maximum. Le point sur les étapes.
Première étape
La première étape, c’est la pyrogazéification, qui consiste à chauffer le bois à très forte température pour provoquer le changement en gaz. ” On va donc faire passer le bois d’un état solide à un état gazeux – on retrouvera en dessous le résidu solide qu’on appelle biochar ou char suivant le niveau de pollution du bois.” Cette opération à haute température se fait de manière endogène – aucun ajout de matière ou d’énergie spécifique n’est nécessaire pour qu’elle réussisse. ” Elle s’autoalimente – c’est pourquoi notre outil tournera en 24/7 toute l’année. “
Seconde étape
La seconde étape consiste à descendre le char en partie solide et la partie gazeuse à température ambiante afin de créer une condensation. Une partie liquide, très polluée, va être à son tour débarrassée des impuretés et réinjectée dans le procédé, tandis que la partie gazeuse restante servira à faire de l’hydrogène ou de l’éthanol.
” Ce gaz est fortement concentré en hydrogène ; soit je l’envoie vers une série de réacteurs gaz à l’eau – système qui permet d’isoler l’hydrogène du reste des gaz, pour obtenir de l’hydrogène sans impuretés ; soit, et c’est notre première option puisqu’il y a un marché pour le moment, je l’utilise pour faire du bioéthanol. “
Une transformation qui fait cette fois appel aux bactéries et à leur fermentation, process mis au point par le laboratoire américain.
” L’ensemble est en effet mis dans une espèce de gros tube dans lequel sera envoyé le gaz par en bas, et l’eau avec toutes les bactéries, par le haut, afin qu’elles soient inoculées par le gaz. En bas, on récupère ainsi des bactéries qui auront grossies de manière exponentielle et en haut, on récupère un gaz pauvre dans lequel il y aura moins d’hydrogène, moins de C02 qu’à la base. “
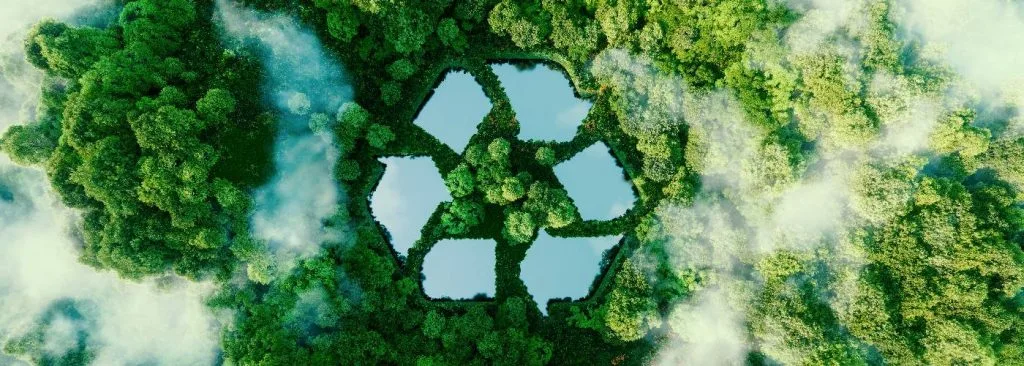
Rien ne se perd, tout se transforme
La partie calorifique – le gaz restant – sera ensuite envoyé dans une chaudière pour combler les besoins du système en vapeur, en chaleur, et 35% des besoins électriques de l’usine.
Quant à la bactérie, engraissée avec le gaz, sa fermentation puis sa distillation produira deux choses : d’un côté, l’éthanol, c’est-à-dire de l’alcool pur, destiné à devenir du bioéthanol, et de l’autre, ce qu’on appelle du lixiviat de distillation, sorte de magma boueux constitué de protéines, d’eau et de boue.
L’idée était de partir sur le même objectif, à chaque étape du procédé. Être le plus efficient possible, en faisant des boucles.
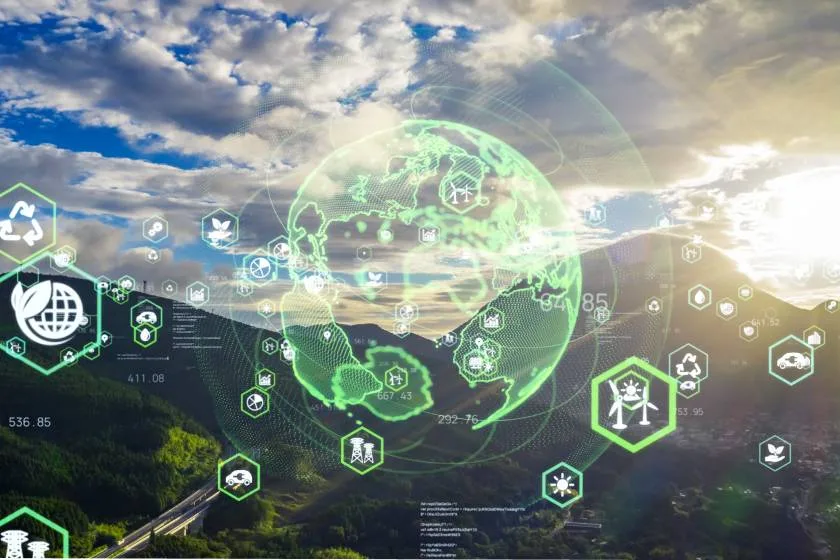
Sur place, une petite station d’épuration permettra alors de séparer la partie aqueuse de la partie boueuse – ” à nouveau l’eau sera réinjectée dans le réseau pour faire une boucle. Une machine, comme un méthaniseur, va nous permettre de sécher la matière boueuse et d’en extraire du méthane qui sera également redirigé vers la chaudière ” précise Vincent Calleja. Quant au résidu restant, ultra protéiné, le chef d’entreprise travaille avec un laboratoire pour le transformer en additif à de la nourriture pour poissons.
Toute cette réflexion a abouti à T.H2. Sur une tonne de bois, tout est valorisé ; on récupère tout, d’une manière ou d’une autre.
Coût de l’opération : 160 millions d’euros, au bas mot.
Des récompenses en pagaille – Normandy4Good, écomaison,… – pour une production ambitieuse : 5% du bioéthanol consommé en France seraient produits par l’usine pilote T.H2 implantée à Blainville-sur-Orne.
Bon à savoir
- 1 million 200 000 tonnes de déchets bois générés par an en Normandie et île de France – 500 000 tonnes sont déjà utilisées dans des chaufferies par exemple.
- Le reste est soit brûlé dans le fond des jardins, soit enfoui, soit exporté.
Validés en décembre 2021, le process et le projet sont toujours en procédure réglementaire en vue d’une pose de la première pierre, espérée en décembre 2024.
Thématiques